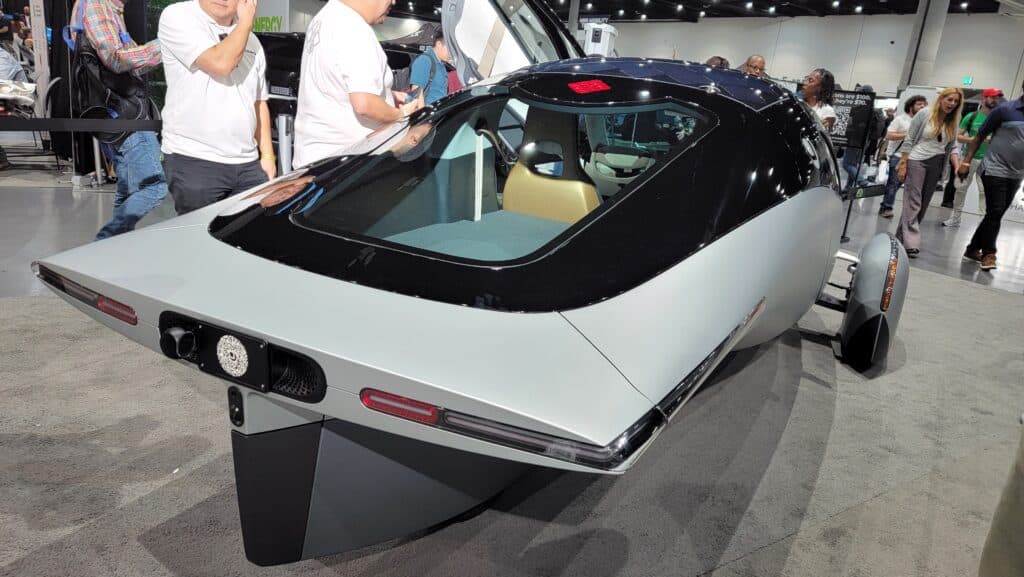
Envision a journey to Las Vegas in a solar-powered, three-wheeled electric vehicle that combines the convenience of a car with the perks of a motorcycle, including HOV lane access. The Aptera, designed by a Carlsbad-based company, offers a unique driving experience with a 400-mile range on a full charge, thanks to its solar-enhanced battery. Its shark-inspired aerodynamic design, tested with NASA’s supercomputers, allows for exceptional efficiency. The vehicle’s structure is influenced by Italian supercars and Formula 1 technology, featuring a strong yet lightweight carbon fiber frame. It boasts impressive performance with rapid acceleration and a top speed of 101 miles per hour, attributed to the simple and powerful electric motors. Aptera aims to optimize energy efficiency by reducing weight and maximizing aerodynamics. Aptera has faced challenges since its inception in 2010, including a failed attempt to secure government funding. However, with renewed federal support for electric vehicles and a successful crowdfunding campaign, the company has over 45,000 reservations and plans to start production by late 2024. The proposed microfactory model promises a streamlined assembly process, capable of producing 40 cars per day. The Aptera vehicle is spacious, with room for cargo or even makeshift accommodation, and is constructed with safety in mind, incorporating the same carbon fiber technology used in Formula 1 cars. Its affordability and capability to recharge via an ordinary extension cord or through solar power make it an innovative addition to the electric vehicle market.
Key Takeaways:
- The Aptera electric vehicle is designed with a focus on efficiency, featuring a solar-powered skin that allows it to recharge while driving and a battery that supports a 400-mile range.
- Aptera’s vehicle borrows design principles from sharks and utilizes a strong carbon fiber frame similar to that used in Formula 1 cars, enhancing its aerodynamics and safety.
- The company plans to produce its vehicles in microfactories capable of assembling 40 cars per day, with a simplified process that takes less than two hours per vehicle.
“”We found that out through computational fluid dynamics. We were like, ‘Oh, that’s what fish do, too,’” Anthony explains.”
More details: here